Keywords: aluminum die-casting, Quality issues of die-casting parts, Porosity of die-casting parts
High-pressure aluminum die-casting parts have the advantages of high dimensional accuracy, good mechanical performance, and high production efficiency. Therefore, they have wide application prospects in fields such as electric vehicles, Telecom equipment, medical equipment, lighting, home appliances, furniture, instruments, and aerospace.
However, under high temperature and pressure, liquid metal flows into the mold cavity at an extremely fast speed from the pressure chamber. The gas is easily entangled into the liquid metal during the flow process and the uneven temperature distribution during the casting process causes defects such as pin hole, porosity, poor fill, crack……etc.
The following is an analysis of common pinhole and porosity quality issues and exploring solutions
1、 Pin hole issue
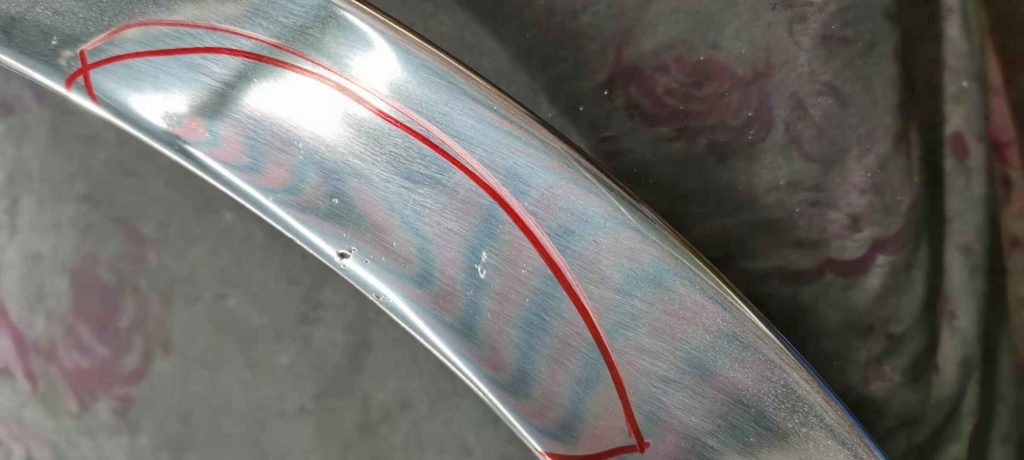
Issue Description:
Pinhole shaped or slightly larger pores occur in castings, which are exposed after machining. Alternatively, pores in areas with high sealing requirements often leak when pressurized by a leak testing machine, or bubbles appear on the surface of the product after coating……etc. The surface of pores is generally smooth, appearing in a circular or circular shape, sometimes isolated, and sometimes clustered together. It can be identified as hydrogen gas pores or gas entangled pores.
Root cause analysis:
- Formation of hydrogen gas pores: Hydrogen gas pores are small, needle shaped, and evenly distributed, and can only be observed after surface processing of the parts. Due to the thin wall of die-casting parts and the fast solidification rate of metal liquid, sometimes hydrogen gas pores are difficult to observe with the naked eye. Water vapor is the main source of hydrogen gas, which may come from furnace gas, smelting tools, aluminum ingots/recycled parts, oil contaminated machining debris, and wet refining agents.
- The formation of air entangled pores: The air entangled pores are circular in shape, clean inside, smooth and glossy on the surface, and sometimes exist alone or clustered together. Entangled air generally occurs in the press-shoot system, runner system, and mold cavity.
Solutions:
- The solution to the formation of hydrogen gas pores:
Refining with GBF degassing and slag removal device; Check if the release agent is sprayed too much and if the concentration of the release agent is within the appropriate range.
- The solution to the formation of air entangled holes:
Select an appropriate slow speed during the low-speed process of the die-casting machine, check whether the turning of the runner is smooth, and whether the cross-sectional area is gradually decreasing. Check if the air venting area is large enough, if there are any blockages, and if the location is at the last filling point to improve the venting. If the mold temperature is too low. The use of vacuum pumping can effectively exhaust the gas entering the mold cavity.
2、Porosity Issue
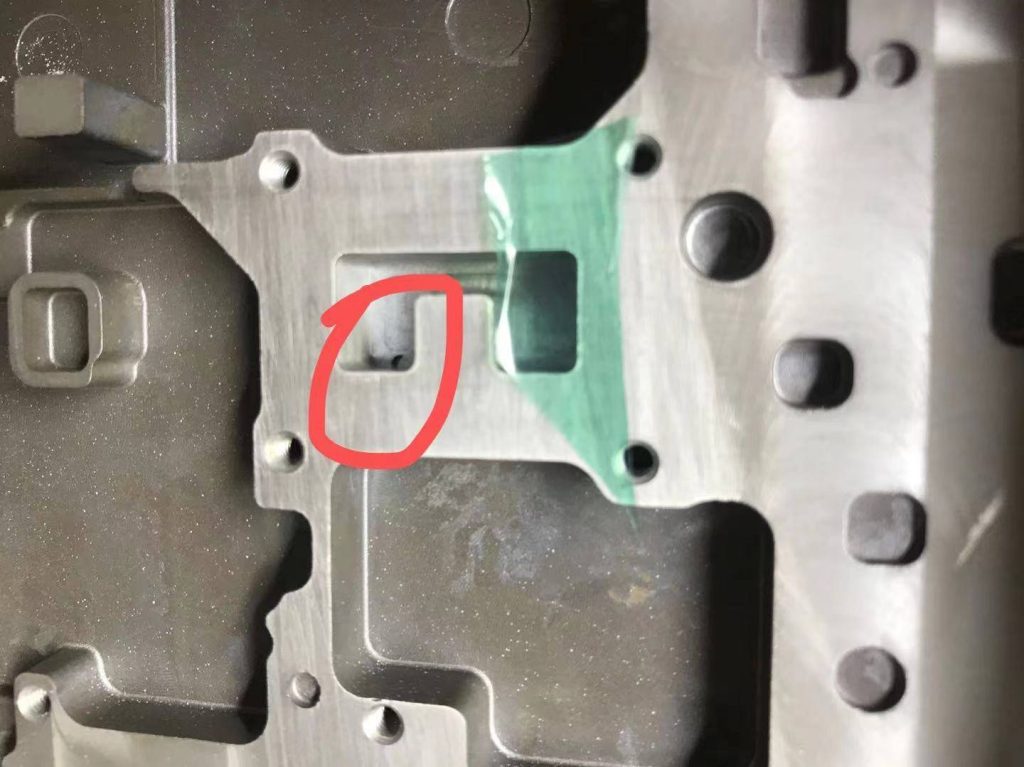
Issue Description:
Porosity (or called Large pores) occur below the surface of the casting, resulting in poor product airtightness and insufficient product strength. Sometimes visible to the naked eye, sometimes detected by an X-ray machine.
Root cause analysis:
Due to the phase change shrinkage that inevitably occurs when the metal melt transforms from a liquid phase to a solid phase after filling. The solidification characteristic of die castings is cooling from the outside to the inside. When some sections of wall thickness of the casting is large, shrinkage and porosity problems will inevitably occur inside. Simply put, the position where the product is relatively thick is characterized by sagging pores formed due to high temperature and slow cooling.
Solutions:
Cut the material at the thicker part of the product. Increase pressure during the pressure-shooting process of the die-casting machine. Change the mold temperature to locally increase cooling, spray release agent, and lower the mold temperature. If the porosity hole is located in the direction of the runner, a new runner can be added to help eliminating the porosity. Adopting extrusion technology and adding extrusion pins, when the porosity hole position is in a semi solid state, forcefully squeeze and supplement it.
—————————————————————————————————————-
If you encounter the above issues of pin hole and porosity issues, please contact us to explore solutions: Contact – wetron (wetronindustrial.com)