Hot chamber die casting is a highly utilitarian manufacturing technique for low melting temperature metals like magnesium, lead, and zinc. This high-pressure die casting method offers numerous benefits to manufacturers like high throughput, low maintenance, and less waste.
The hot chamber die casting process has widespread applications owing to its diverse material compatibility. Some of its applications are in industries like automotive, electronics, aerospace, etc., which is just a glimpse of how essential it is.
In this article, we will explore the ins and outs of hot chamber die casting. Our discussion will center on its process, components, advantages and disadvantages, and industrial applications. In the end, we will also briefly compare it with another popular die casting process, cold chamber die casting, to further illustrate its importance.
Contents hide
I What is Hot Chamber Die Casting?
II Components of Hot Chamber Die Casting
III Hot Chamber Die Casting Process
IV Advantages and Disadvantages of Hot Chamber Die Casting
V Materials for Hot Chamber Die Casting
VI Applications of Hot Chamber Die Casting
VII RapidDirect – Produce Your Die Casting Parts
VIII A Brief Comparison between Hot Chamber and Cold Chamber Die Casting
What is Hot Chamber Die Casting?
Like any casting process, hot chamber die casting requires a die with a cavity that is filled with molten metal. After the metal cools down and solidifies, the die opens and ejects the final part, completing a process cycle. This cycle then continues

The main distinguishing feature of hot chamber pressure die casting is its integrated furnace and die setup. Normally, in processes like cold chamber die casting, the furnace is a separate, standalone machine from the die so the intense heat does not damage the die casting machine.
Since hot chamber die casting is a special process for only low-temperature metals, it is possible to place the furnace right next to the die without any risks of damage. This is incredibly efficient as there is no time wastage in transporting the molten metal from the furnace to the die. Instead, the injection mechanism directly injects the metal from the furnace into the die.
In addition to being quicker, it produces high-quality parts at a lower cost, as we will discuss shortly.
Components of Hot Chamber Die Casting
The hot chamber die casting machine is complex equipment with multiple components. We will briefly explain them one by one.
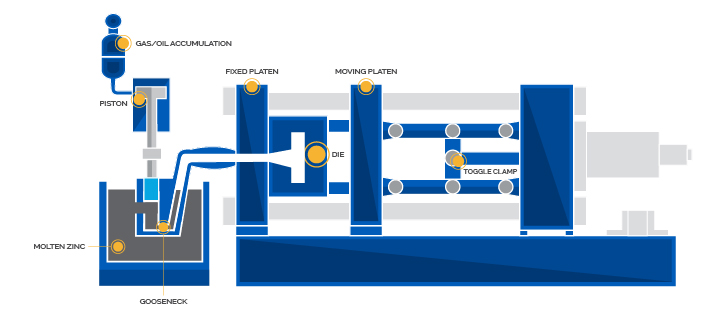
Furnace
The most important element of this machine is its built-in furnace. The furnace has a combustion chamber to burn fuel and produce extreme temperatures to melt the raw materials. In hot chamber casting, the furnace is in close vicinity of the die, as shown above.
Gooseneck
This is an essential component that is unique to hot chamber casting setups. The gooseneck links the injection mechanism to the feed line through which the molten metal travels into the die. It is submerged in the molten metal pool. As a result, it must have a high thermal resistance. Consequently, it is ideal to manufacture it from high-quality cast or forged steel. It contains a cylindrical lining that houses the hot chamber and the plunger, which are part of the hydraulic injection mechanism. Furthermore, most goosenecks are replaceable as their quality still deteriorates over an extended period under the intense working conditions.
Nozzle
The nozzle regulates the flow of the molten metal through the gooseneck into the die. It acts as a gateway for the metal to enter the mold in a smooth, well-directed manner. Also, any extra raw material at the end of the casting cycle travels back into the furnace through the nozzle.
Hydraulic Plunger/Piston
This component transports the molten metal into the die and maintains it at high pressure. The plunger traverses up and down through the hot chamber. It power source is an oil or gas hydraulic cylinder.
Die
Finally, the die/mold itself. It contains the cavity and ejector pins to eject the part. Moreover, it might house additional components like cores, depending on the part geometry. The die in the hot chamber die casting process is the same as other casting methods.
Hot Chamber Die Casting Process
Now that the various components of a hot chamber die casting machine are clear, it is a good point to discuss the process.
The hot chamber die casting process has four main steps as follows:
- Hot Chamber Filling: The plunger moves upwards to open the liquid intake port. As soon as the port opens, liquid metal from the furnace fills up the hot chamber of the hydraulic plunger mechanism inside the gooseneck.
- Injection: The hydraulic plunger then moves down, pushing the liquid contents inside the hot chamber into the die cavity. The liquid metal travels through the nozzle into the cavity and fills it up.
- High-Pressure Die Casting: After filling the cavity, the plunger keeps applying pressure to the molten metal to achieve a high-quality casting. Typical pressures range from 5-35 MPa, depending on the metal and the geometry features like size, contours, etc.
- Cooling: The molten metal then cools down inside the cavity. After the cooling cycle ends, the plunger retreats to its initial position and the die opens to eject the part. The part is then ready for post-processing and the machine is ready for a new casting cycle.
Advantages and Disadvantages of Hot Chamber Die Casting
Hot chamber die casting has numerous pros and cons that manufacturers must know to make informed decisions. Let’s take a look at what these are.
Advantages of Hot Chamber Die Casting
We will begin with the benefits of hot chamber casting. It is popular owing to its speed, cost-effectiveness, quality, and longer tool life.
Quick Production Cycle
Hot chamber pressure die casting is a low temperature casting process. This leads to significant time-saving as melting and solidifying of the molten metal both are quick. Moreover, since the melting pot of the furnace is integrated into the setup, the time wasted in carrying molten metal to the die is also saved.These factors allow an impressive throughput of up to 15 cycles per minute.
Cost-Effective
There are several reasons for this process being cheaper than techniques like cold chamber die casting. First of all, its high productivity directly increases profitability. Furthermore, the machinery has a smaller footprint due to its built-in furnace-there is no standalone furnace to take up extra space. Moreover, manufacturers also save costs on the equipment and labor responsible for moving molten metal from the furnace to the die.
Longer Tool Life
This is an extension of the previous point. The mold in hot chamber die casting does not bear high temperatures. So, it wears slower and survives longer. This saves money and logistic effort for the manufacturer.
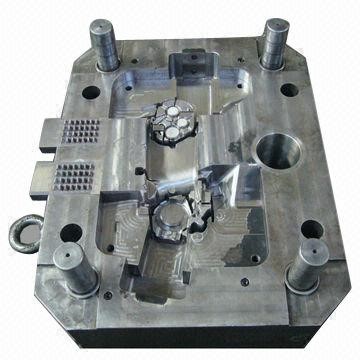
Less Material Waste
The built-in furnace minimizes material wastage by fully utilizing it. The raw material is sometimes spilled and wasted during transportation, which is not an issue with this setup.
Disadvantages of Hot Chamber Die Casting
Benefits and losses go hand in hand. Now, it is time to highlight some of the disadvantages of hot chamber die casting.
Limited Material Choice
The application of hot chamber casting is limited to low melting point metals like zinc, magnesium, tin, etc. As a result, engineers are left with a limited material portfolio if they decide to go for hot chamber die casting.
Not for Low-Volume Production
The financial viability of die casting only makes sense when the volume of production is high. This is due to the high costs of die production. If engineers are dealing with a low-volume project, it is better to do a detailed cost-benefit analysis to judge the feasibility of the hot chamber method before making final decisions.
This concludes our pros and cons section. In most cases, there is a direct competition between die casting and injection molding as both are molding processes. Being knowledgeable on both is a must if you want to maximize profitability.
Materials for Hot Chamber Die Casting
Hot chamber casting is compatible with low melting point metal alloys. In this section and the next one, we will introduce some of these materials and highlight their main applications.
Zinc
Zinc is inarguably the most popular metal when it comes to hot chamber pressure die casting. The zinc casting boasts high strength and hardness along with good wear properties. Its alloys melt at a relatively low temperature of around 420oC, making it compatible with this process.
It also possesses good electrical and thermal conductivity, making it an exceptional choice for components containing electronic circuitry. Moreover, it has high fluidity in molten form, which improves its dimensional tolerance and allows for the manufacturing of complex geometric features like thin walls.
Finally, it is a cheap raw material with good recyclability. Overall, it is a great option for die casting.
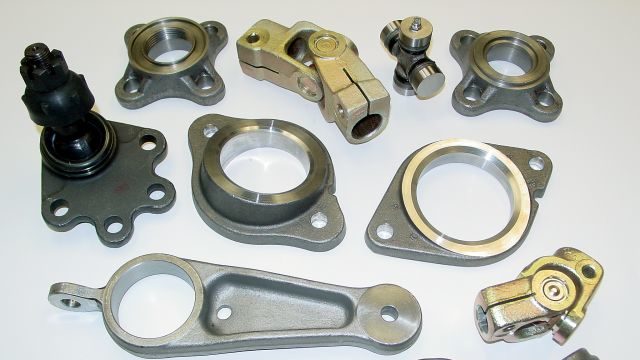
Magnesium
Magnesium is another strong candidate for hot chamber die casting setups. It is lightweight, strong, and recyclable. Furthermore, it also sports high electrical and thermal conductivity like zinc. These qualities give it the same advantages of high dimensional accuracy and suitability for thin wall structures. It also has good shielding capability against radio frequency and electromagnetic interferences, which is a unique property to have.
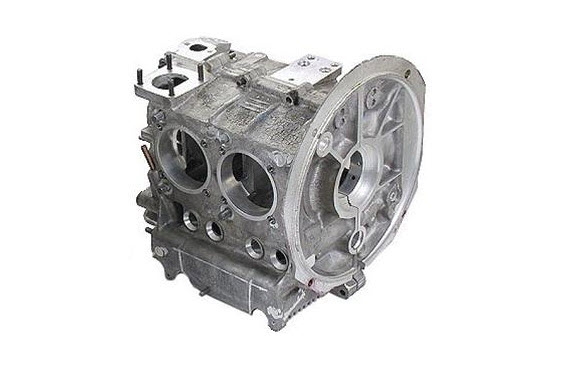
Why Not Choose Aluminum Alloys
Aluminum alloys have higher melting points than zinc and magnesium alloys, typically at least 660oC. This temperature is too high for the low-temperature hot chamber casting process.
At these temperatures, having the furnace connected to the die casting setup is no longer feasible. One should expect a rapid drop in tool life and manufacturing accuracy if one attempts to die cast aluminum alloys (or any other high melting point alloys) with a hot chamber setup.
Applications of Hot Chamber Die Casting
In this section, we tie the materials from the previous section to their applications. Although their applications cover a wide range of industries and are too many to discuss on this platform, we will try to cover the most prominent ones.
- Automotive: Die casting in the automotive industry is a huge market. Hot chamber die casting products include engine and transmission components made from zinc alloys and electronic components like rearview mirror enclosures. High-performance cars oftentimes use lightweight magnesium alloy castings for weight reduction.
- Enclosures for Electronic Devices: Magnesium and zinc alloys have great electrical conductivity. Consequently, they are very useful for making products like smartphone components and enclosure bodies for integrated circuitry.
- Decorative Items: Some aesthetic-looking metal alloys like tin are quite popular for decorative items like jewelry items and household decorative products.
- Aerospace: Zinc/magnesium alloys are useful due to their weight-reducing capabilities. Engineers sometimes incorporate tin alloys in manufacturing gas turbine components and motors for aerospace vehicles.
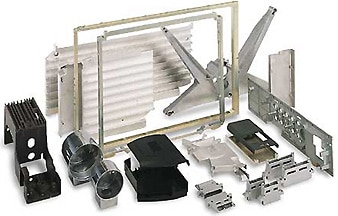
RapidDirect – Produce Your Die Casting Parts
Are you in need of die cast parts? RapidDirect is your manufacturing partner offering remarkable services in die casting. With RapidDirect, you are guaranteed the best customer service by our expert team. At our state-of-the-art manufacturing establishment, we provide you high-quality die cast parts with unmatched precision and structural integrity.
We will assist you in choosing the best materials for your die casting applications. Moreover, we will also recommend you the ideal casting method, from amongst hot chamber, cold chamber and others, for your die casting project.
We believe in the power of customer service. To further enrich our client relations, we also offer a comprehensive Design for Manufacturing (DFM) analysis to our customers to facilitate their decision-making process. So, try RapidDirect now.
Try RapidDirect Now!
All information and uploads are secure and confidential.
A Brief Comparison between Hot Chamber and Cold Chamber Die Casting
Hot chamber die casting and cold chamber die casting are the two main types of die casting methods. We know all about the former by now. Let us briefly compare them as well for a better understanding of the topic.
- Furnace: It is clear from the above discussion that the furnace and die are part of a single unit in the hot chamber process. For cold chamber die casting, it is a completely independent unit, oftentimes at a different location on the factory floor.
- Cycle Times: Cold chamber die casting has higher cycle times, and consequently lower productivity, due to long melting and cooling times.
- Materials: The materials for the hot chamber process are zinc, magnesium, tin, etc. Higher melting temperature metals like aluminum alloys are common in cold chamber die casting.
- Safety Measures: Hot chamber casting is generally safer due to the lesser movement of molten metal and lower temperatures. Manufacturers have to invest more in worker and equipment safety when using cold chamber casting setups.
- Investment: Manufacturers usually have to spend more on cold chamber die casting. The furnace and die casting setup cost a lot, energy costs are higher, and maintenance costs are also comparatively high due to more temperature-related wear and tear. Moreover, tool life is lower as well, which is a huge expense in die casting.
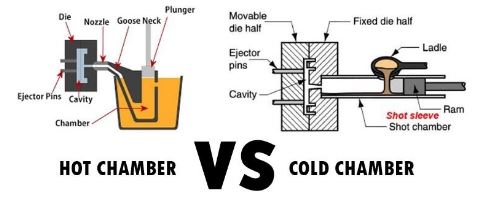
Conclusion
Hot chamber die casting is a core manufacturing technology in the modern industrial world. It is unique due to its high-pressure, low-temperature combination that is highly suitable for low melting temperature metal alloys, a very specialized application.
In this article, we went over it in great detail, discussing its process and machine components. It has various benefits that enhance profitability for manufacturers and very few disadvantages. Some of the materials it works well with include zinc and magnesium alloys, which have innumerable applications in sectors like automotive, aerospace, electronics, etc.