One process will never suit every project, which is why we offer multiple solutions to your die casting needs. This ensures the right process is always used for the right application. Our zero-defect quality goal is one of the reasons why we are the preferred supplier to many of the world’s leading manufacturers. Ultimately we believe that if you can imagine it, we can cast it.
INTRODUCTION
Die casting machine, aluminum raw material, and die casting mold tool are the three basic factors to produce a die casting parts. For an aluminum die casting process, it particularly requires to use a cold chamber casting machine under a high pressure.
During the aluminum alloy die casting process, the raw aluminum material is pre-molted in a furnace that set aside of die casting machine. Then the molted material is transferred from furnace to die casting machine by a moveable ladle. After that, those material will be forced into the die casting mold cavity where the material cools and solidifies to obtain desired die casting products. Here below are the process step breakdown.
If you have needs of custom metal parts, Wetron is a die casting service manufacturer that can help. Since 2008, we’ve hold our engineering team and equipment to a high standard to continually deliver strong and durable parts and prototypes. To ensure legendary quality, we operate strict die casting process that ensures that your custom requirements are being met. We can’t wait to receiving the your technical drawing and inquiry, and we will be there to service you any time you need.
Are you still looking for the Aluminum Die-Casting? Please contact us below : https://wetronindustrial.com ; contact person : sales@wetronindustrial.com
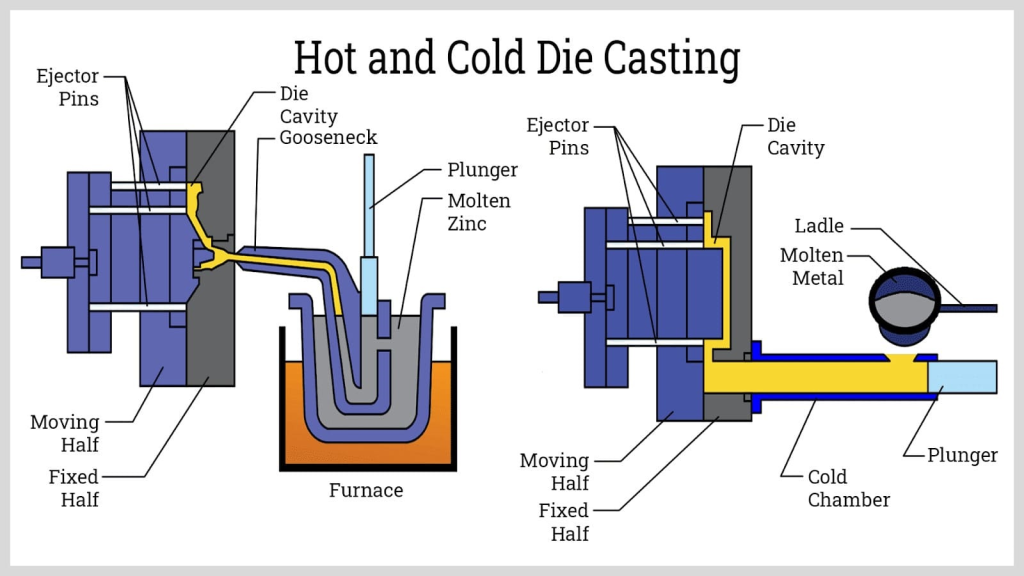
Our Aluminum Die Casting Flow-chart
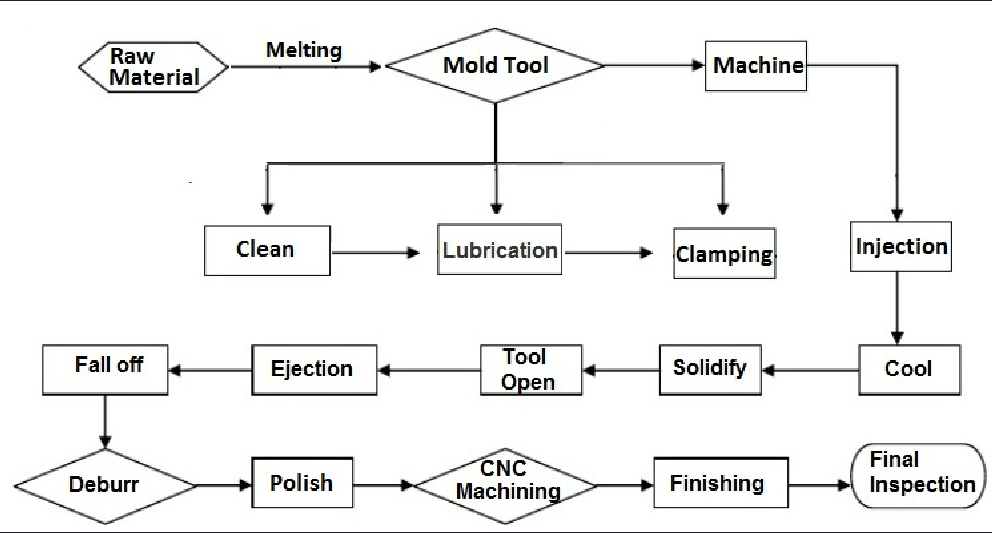
- Step 1. Material Melting
Since aluminum has a very high melting point(660.37 °C) that can’t be melted inside a die casting machine directly. This is why we need to pre-melted it with a furnace that attached with a die casting machine.
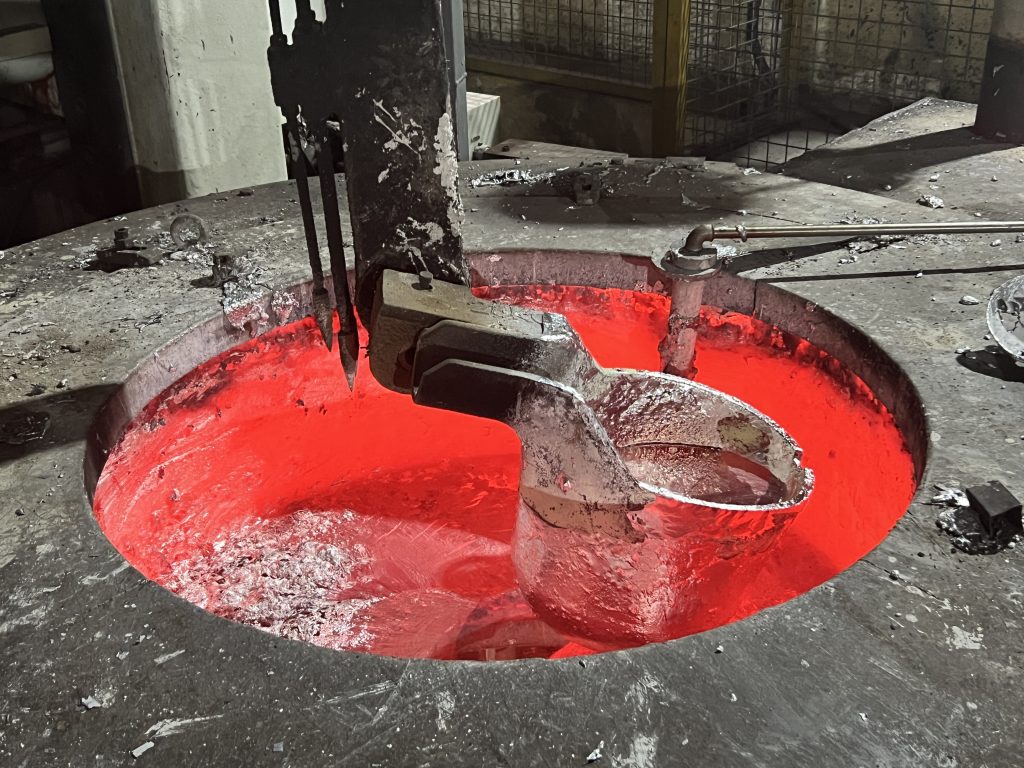
- Step 2. Mold Tool Mounting and Clamping
It’s almost similar to injection molding, the die casting process also needs a mold tool for casting process. Therefore we need to mount the die casting mold tool on a cold die casting machine.
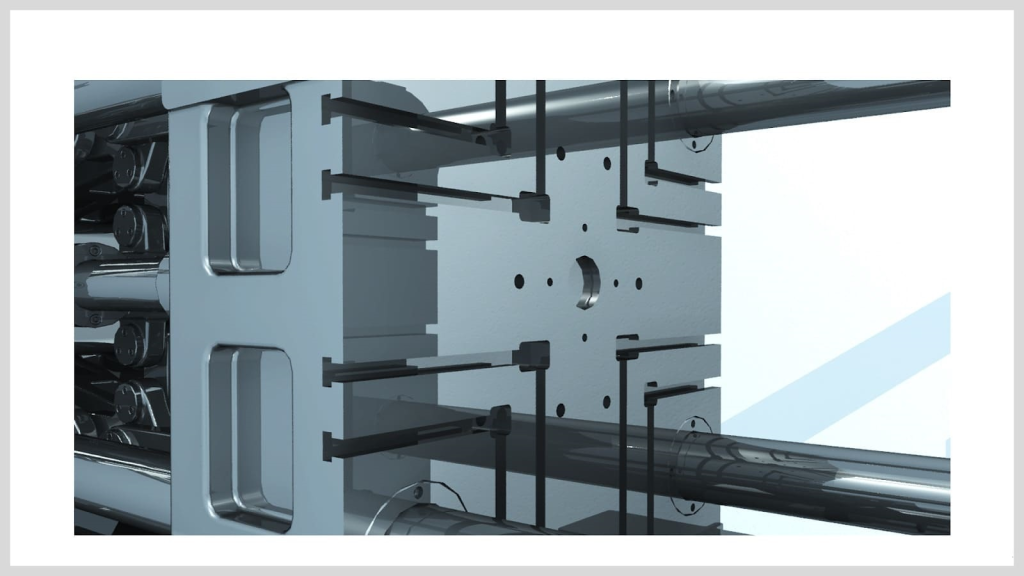
- Step 3. Injection or Filling
The molten material is transferred from furnace to die casting machine by a moveable ladle. In this stage, the material will be poured and forced into the die casting mold cavity where the material cools and solidifies to obtain desired die casting products.
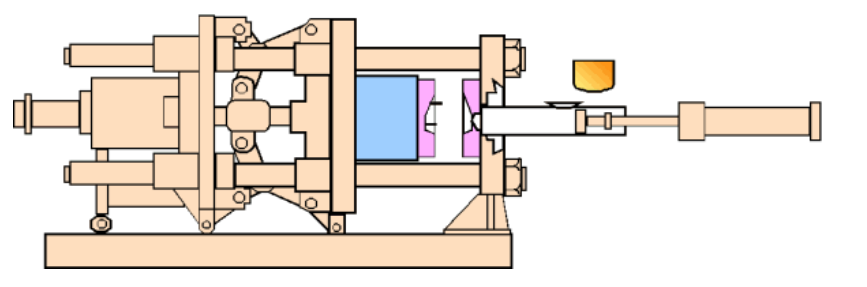
- Step 4. Cool and Solidification
After the die casting mold tool is fully filled with molten material, it takes 10 ~50 seconds to cool and solidify( it depends on part structure and size).
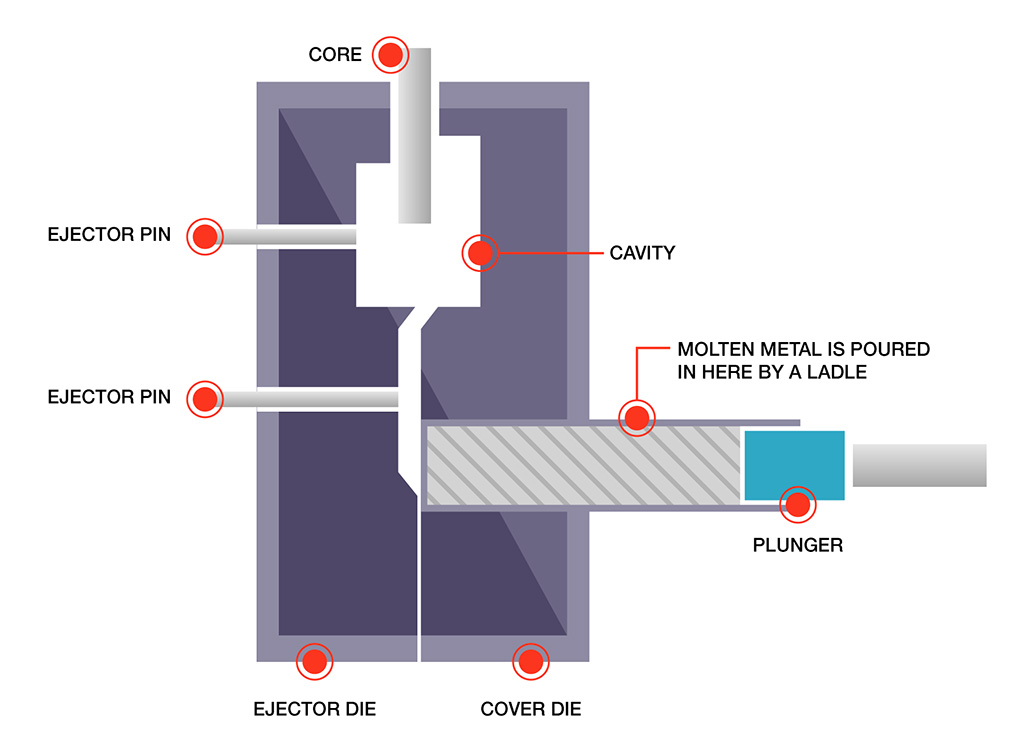
- Step 5. Part Ejection
When the mold opens, the casted parts would be ejected off by ejection pins from die casting mold tool. Then the raw casted parts is ready.

Die Casting Process Simulation and Analysis
- Aluminum Die Casting Simulation
We utilize professional casting analysis software(Cast-Designer) to study the speed and switching point of high-pressure casting process, it is beneficial to reduce the oxides and gases that brought into the mold cavity. The simulation can clearly anticipate any injection issue during the first-second speed of the hammer in the injection tube, and understand how the molten metal flows in the pressure chamber.
- High Pressure Die Casting Simulation
With professional simulation software, we can accurately simulate the filling and air exhausting process of various die-casting alloys, and accurately determine the area where the gas is exposed and the exhaust gas is not smooth. In addition, “Gas Lead Time” and “Maximum Volume Pressure” can be used for accurate single-graph risk viewing.