High Pressure Casting (HPDC)
High pressure casting is commonly referred to as die casting, where aluminum liquid is poured into the pressure chamber and filled with the mold cavity at high speed through its pressure, causing the aluminum liquid to solidify under pressure to form an aluminum casting. High pressure die casting is a method in which liquid or semi solid metals or alloys, or liquid metals or alloys containing reinforcing phases, are filled into the cavity of a die casting mold at a high speed under high pressure, and the metal or alloy solidifies under pressure to form a casting. The commonly pressure during die casting is 400-500MPa, and the metal filling speed is 0.5-120m/s. Therefore, the filling time of the molten metal is extremely short, and it can fill the mold cavity within approximately 0.01-0.2 seconds (depending on the size of the casting part). Therefore, high-pressure and high-speed are the fundamental differences and important characteristics between die-casting and other casting methods.
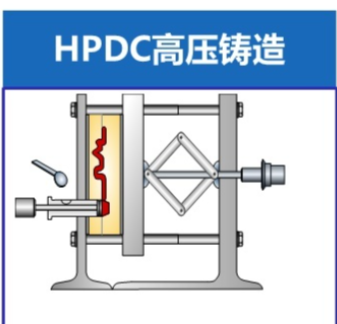
There has the following properties of die-casting aluminum alloys process:
- Well thermoplastic properties should be achieved at low heat and near liquid-solid temperatures to achieve complex cavity filling, form a good casting surface, and avoid the occurrence of shrinkage defects;
- A smaller linear shrinkage rate avoids cracks and deformation during the die-casting process, improving the dimensional accuracy of the product;
- A smaller solidification temperature range facilitates rapid and simultaneous solidification, reducing the number of internal shrinkage pores and other defects;
- Good high-temperature thermal strength to avoid thermal cracking or severe deformation during mold opening;
- Good casting/mold interface performance, no chemical reaction with die-casting molds, low affinity, avoiding adhesion and alloying reactions at the casting/mold interface;
- Good physical and chemical properties, difficult to absorb and oxidize under high temperature melting state, can meet the needs of long-term insulation in the die-casting process.
Low Pressure Casting (LPDC)
Low pressure casting is carried out in a sealed crucible (or sealed jar), where dry compressed air is introduced. Under the action of gas pressure, the metal liquid enters the sprue and rises along the riser, smoothly entering the mold cavity through the sprue, and maintaining the gas pressure on the liquid surface inside the crucible. Until the casting completely solidifies. Then relieve the gas pressure on the liquid surface and allow the non solidified metal liquid in the riser to flow back to the crucible. Open the mold again and remove the casting. This casting method has good shrinkage and dense casting structure, making it easy to cast large and complex thin-walled castings without the need for risers. The metal yield reaches 95%. No pollution, easy to achieve automation. But the equipment cost is high and the production efficiency is low. Generally used for casting non-ferrous alloys.
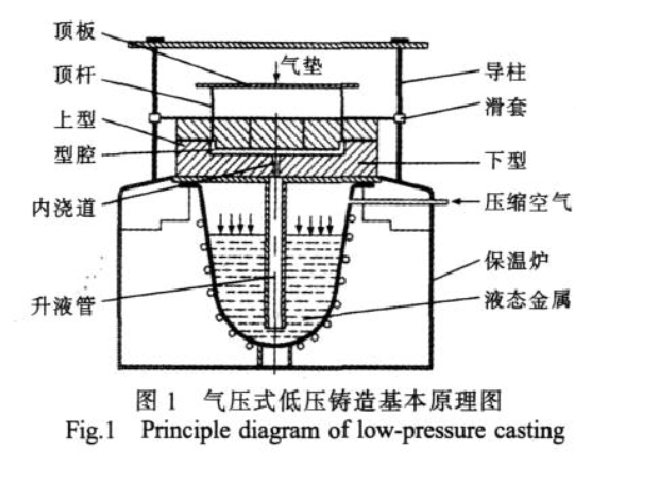
The characteristics of aluminum alloy low-pressure parts are:
1. The surface difference of the product is stronger than that of gravity parts. 2. The internal pores of aluminum castings are less and can be subjected to heat treatment. 3. The product has high air tightness, high casting strength and surface hardness, but low elongation and dry weight. 4. The mold cost is low and the service life is low. 5. Low production efficiency, far lower dry die casting. 6. The process is complex, with high requirements for dry production and high-quality castings. 7. Low fluidity special aluminum alloys can be used. Simply put, low pressure is the compromise between high pressure and gravity.
Gravity Casting (GDC)
Gravity casting refers to the process of injecting aluminum liquid into the mold by gravity under the action of Earth’s gravity. The generalized gravity casting includes sand casting, metal casting (steel casting), lost foam casting, and so on. The narrow meaning of gravity casting specifically refers to metal mold casting. Metal mold casting can be divided into vertical manual casting, and inclined casting is now most commonly used in metal molds (steel molds) casting. The mold is made of heat-resistant alloy steel, and the strength, size, and appearance of the cast aluminum castings are higher than those of other casting processes. The aluminum liquid in gravity casting is generally poured manually into the gate, relying on the self weight of the metal liquid to fill the mold cavity, exhaust, cool, and open the mold to obtain the sample.
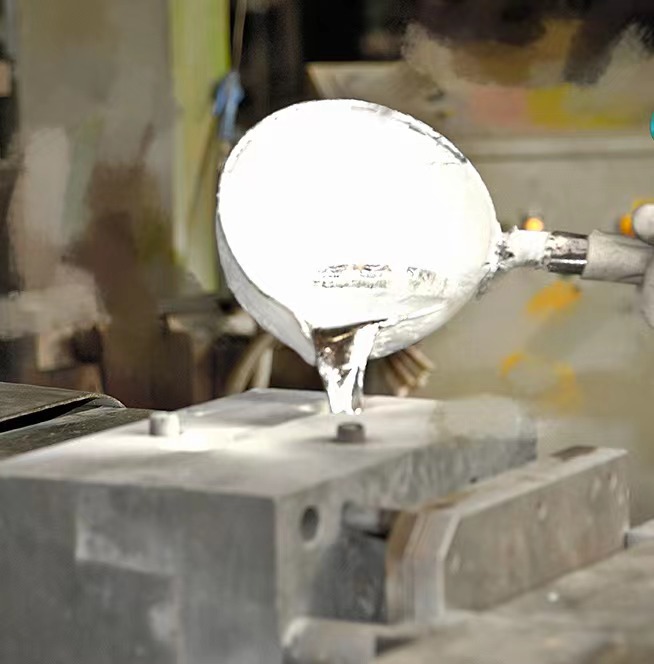
The characteristics of aluminum alloy gravity casting parts are as follows: 1. The surface smoothness of the product is not high, and it is easy to produce pits after shot blasting. 2. Aluminum castings have fewer internal pores and can be subjected to heat treatment. 3. The product has low density and slightly poor strength, but high elongation. 4. The cost of the mold is low and the mold has a long service life. 5. Low production efficiency increases production costs. 6. The process is relatively simple and not suitable for producing thin-walled parts. 7. Low fluidity special aluminum alloys can be used.
Sand Casting
When “sand casting“, the lower half of the mold is first placed on a flat plate, and the sand box is filled with sand to compact and scrape flat. After the lower mold is completed, the sand mold is flipped 180 degrees. The upper half of the mold is placed, and the parting agent is sprinkled. The upper sand box is placed, and the sand box is filled with sand to compact and scrape flat. The upper and lower half of the mold are flipped 180 degrees, and the upper and lower half of the mold are taken out separately. Then, the upper mold is flipped 180 degrees and the lower mold is closed. After the sand mold is completed, wait for pouring.
The sand mold material must have a certain adhesive strength in order to be molded into the desired shape and be able to resist the erosion of high-temperature molten iron without collapse. In order to mold the sand mold into a cavity that matches the shape of the casting, it is necessary to first make a model out of wood, called a wooden mold. After the hot molten iron cools down, its volume will decrease. Therefore, the size of the wooden mold needs to be increased according to the shrinkage rate based on the original size of the casting, and the surface that needs to be machined should be correspondingly thickened.
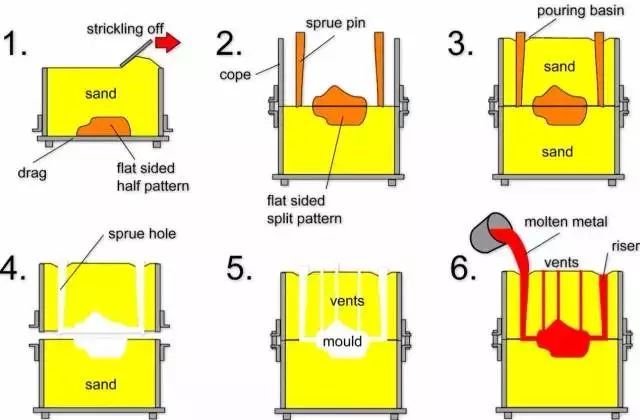
Have a Die Casting Idea?
Wetron are experts with over 15 years’ experience in the manufacture of high-quality aluminium die casting parts provider, across a wide range of applications and industries.
We can help you to choose the best process to benefit the final application of your component.